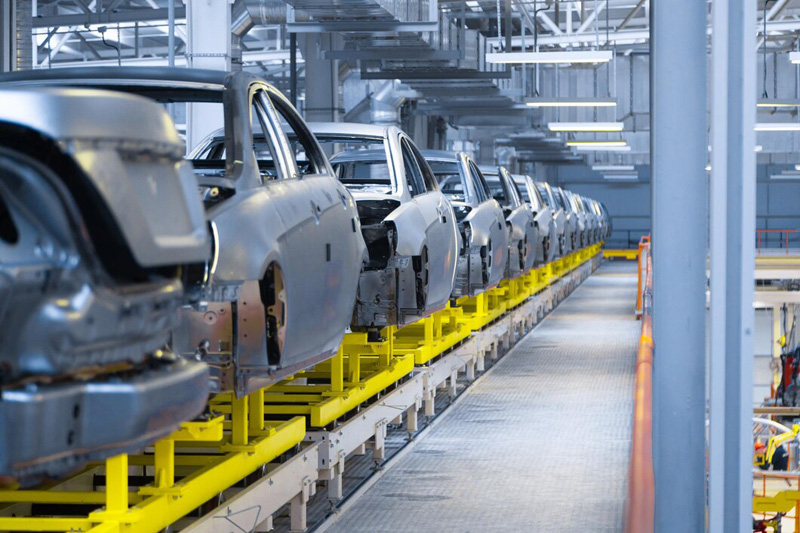
一、洁净度等级与分区设计
锂电池生产对环境洁净度要求严苛,需根据工序特性划分功能区域。电芯封口前的大环境通常需达到十万级(ISO Class 8),关键工序如极片分切、叠片等需提升至万级(ISO Class 7)甚至千级(ISO Class 6)。不同区域需通过压差控制(5-15Pa)和独立气流组织避免交叉污染,例如注液车间采用-40℃露点控制,并配置转轮除湿机 + 冷冻除湿组合系统。
二、温湿度精准管控
温度控制:
涂布工序需维持在 25±1℃,干燥工序则需升温至 60℃,需采用冷水机组或精密空调实现分区温控。
湿度控制:
湿度是锂电池生产的核心参数。搅拌、涂布区域相对湿度需≤30%,叠片、注液等关键环节需≤10%,露点温度≤-45℃。除湿机组是核心设备,需配合车间密闭性设计(如双层真空玻璃窗、不锈钢风管)确保稳定性。
三、防静电与防爆设计
静电防护:
人员需穿戴防静电服(表面电阻 10⁶-10⁹Ω)、佩戴腕带,设备接地电阻需<1Ω。高风险区域(如卷绕工位)需安装离子风机,表面静电压控制在≤100V。
防爆措施:
电解液存放区、注液间等危险区域需独立防火分区,采用岩棉板隔墙、防火门及防爆型电气设备。车间需设置可燃气体报警装置,事故通风换气次数≥12 次 /h。
四、废气处理与环保要求
废气处理工艺:
涂布工序产生的 NMP 废气需通过化学喷淋 + 活性炭吸附处理,注液废气需增设电解液吸附装置。废气排放需符合《电池工业污染物排放标准》(GB30484-2013),非甲烷总烃浓度≤50mg/m³。
节能与可持续性:
采用沸石转轮 + 催化燃烧(CO)技术,可实现 95% 以上的净化效率,同时回收余热降低能耗。例如江苏某项目通过该工艺年运行成本降低 30%。
五、材料选择与施工规范
建筑材料:
低湿度区域采用岩棉板隔墙、玻镁岩棉板吊顶,地面根据工序需求选择环氧树脂自流平或不锈钢花纹板。门窗需密闭性设计,如成型钢制净化门和双层真空玻璃窗。
施工要点:
风管采用角铁法兰连接,注液区需不锈钢材质;照明系统采用 LED 灯具,照度控制在 250-300Lux,并配置应急照明。
六、智能监控与验收标准
智能化管理:
引入 PLC 控制系统实时监测温湿度、洁净度等参数,关键设备(如除湿机组、风机)可远程调控。例如某项目通过云端数据优化,能耗降低 20%。
验收要求:
竣工后需进行尘埃粒子检测(激光粒子计数器)、压差测试及温湿度稳定性验证,确保符合 GB50073-2013 等标准。
七、行业趋势与合规建议
随着欧盟《电池与废电池法规》等政策实施,锂电池生产需强化碳足迹管理和材料回收。例如,2027 年锂回收率需达 50%,企业需在净化工程中预留技术升级空间。同时,建议采用绿色建材(如 B1 级防火保温棉)和雨水收集系统,响应可持续发展要求。